Drilling & Instrumentation Installation Collaboration
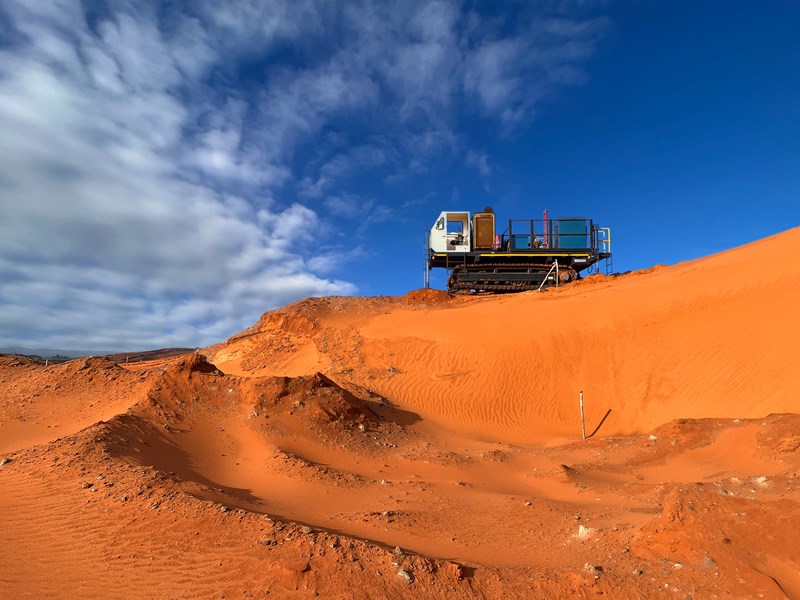
Geomech Africa was recently contracted for a project on a tailings facility in South Africa. The project involved conducting 21 CPTu tests in November of 2023, to determine ideal drill locations, and then drilling these boreholes and installing a monitoring system to assess the stability of the dam embankments.
PROJECT DETAILS:
Equipment: Colossal CPT-150, YWE D90 drill rig.
Drilling started: CPTu Testing (November 2023), Drilling (February 2024)
Holes Drilled: 17
Drill Depths: Depths ranging between 4 meters and 19 meters.
Drilling Method: Wash borehole drilling.
Hole Size: HXC-size (120mm diameter).
Purpose: Installation of Vibrating Wire Piezometers.
DRILLING AND MONITORING SYSTEM INSTALLATION:
After the initial CPT assessment, the received scope of work required standard drilling to be conducted at the 17 drill locations. Our skilled drillers ensured that no major issues were encountered. Some access excavations were required to facilitate drilling on the tailings to reach certain drill positions.
The boreholes were drilled to allow for the installation of 90mm slotted PVC casings to prevent collapse and ensure proper placement of the Vibrating Wire Piezometers.
Terra Monitoring technicians then installed the piezometers, followed by digging one-meter trenches to lay sleeves for wiring that would connect to 9 designated Node points. The 18 installations provided data to the gateway via an internet connection, allowing the data to be recorded in near-real-time increments with the data accessible at the main control room.
REPAIR OF DAMAGED STANDPIPE PIEZOMETERS:
Following the drilling, repairs were made to several damaged standpipe piezometers that had been pushed over and filled with sand. The broken casings were extended above ground level and flushed with pressurized water.
As part of the rehabilitation of some of the casings, we had to install 4 x Y stand poles, each 2,4 meters in length, into the sand to support the casted concrete block. In one location, hammering the poles to the required depth proved challenging due to hardened sand. It took additional time and elbow grease to advance the Y poles to the required depth.
The investigation revealed a blockage in this particular piezometer at 2,9 meters, including the 1,4-meter standpipe. Due to the hardened sand, the Y pole diverted and cut through the PVC piezometer casing. Lowering a camera down the casing confirmed our suspicion. To address this, a TLB was brought in to access the side of the blockage underneath the concrete block. The damaged section of the casing was cut out and replaced, with a slight diversion to avoid the Y pole.
Following repairs, the piezometer was successfully tested, and the sand was backfilled, resulting in a fully functional standpipe piezometer returned to the client.
This project successfully showcased our drilling capabilities, the installation of a new monitoring system and the repair of existing piezometers, ensuring the continued stability assessment of the tailings facility.
Plot 28 Central Road
Sunrella, Lanseria
Gauteng
South Africa
Tel. +27 (0)861 436 632
Email. info@geogroup.co.za