Drillers in the Mist
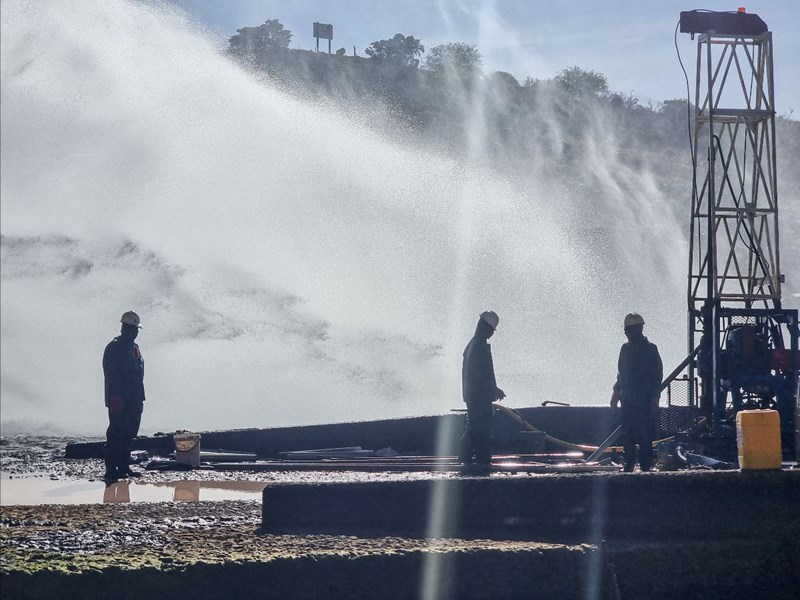
DRILLERS IN THE MIST
By Brett Mannix (Western Cape Regional Manager)
There’s something unusual about preparing yourself in a site mud room with gumboots and a rain suit over your standard required PPE when the ambient temperature is in the mid-thirties, and the conditions are equivalent to that of a tropical rainstorm. This was the case on a recent drilling project the Geomech Africa team took on in the Western Cape.
The requirement was simple, fourteen boreholes were to be drilled in the Apron at the foot of the dam wall. Not so simple it would seem, as the Apron has elevated platforms to the West of the wall, a large stilling pond at the foot of the wall, and a Hydropower plant to the East of the wall. All of which are surrounded by retaining walls and the outflow into the local stream.
The aim of the drilling project was to determine the concrete thickness between the Apron and the contact point with the natural ground that the Apron has been founded on. As challenging as the drilling is in this area given the extreme hardness of her rock, the supply of water, and having to use surface recirculation sumps, access was going to be the major obstacle.
There were three challenges when it came to access, first being the stepped elevated platforms each rising by 1.50m from each other. Secondly, the stilling pond which stepped down 1.50m between each level and then finally into the bottom portion of the stilling pond, which was over 2m deep, all submerged in water, and thirdly the Eastern side of the Apron and hydropower plant which was separated from the main Apron with a 1.5m high retaining wall of turbulent outflow.
A 60-ton crane perched high up on the Western bank of the dam wall with a team of expert riggers enabled us to carefully and precisely place the smaller of the drill rigs, 2.50 tons, and all its drilling equipment on the topmost platform. After relocating the 60-ton crane halfway down the access road to the top of the dam wall, we managed to sling the bigger & heavier drill rig, 4 tons, to its borehole position which was two platforms lower than the smaller rig. All this would have to be done once more when each rig had finished their first boreholes, but at least we had a suitable and safe plan for the first of three access challenges.
The next challenge would require that we mobilized another of the larger drill rigs and our MERC 4x4 Crane truck carrying all the equipment through the turbulent outflow of the hydropower plant and through the 1.50m high retaining wall. The task required the use of a 30-ton excavator to build a road through the outflow area as the turbulent water had created deep channels. Once the road was completed the 30-ton excavator had to raise the four 2.50m long concrete beams to allow our drill rig & truck through, all of which had to be done as fast and as safely as possible to avoid delays and downtime of the hydro plant. The drill rig tracked itself across the levelled area and onto the Apron with the MERC 4x4 Crane truck following. Once the truck had been off-loaded, it returned to the loading area while the excavator replaced the concrete beams stopping the outflow water from flooding the Western part of the Apron. Fortunately, the various platforms on the West had concrete ramps between them which allowed for tracked access from borehole to borehole.
To limit the level of the water and to stop the Apron from flooding, the flow of water through the foot valve had to be reduced during drilling. The flow was increased in the evenings to assist with water supply downstream, which introduced a new challenge of pumping out the excess water that had flooded the drilling area overnight.
The last few boreholes that were situated on the Apron were adjacent to the stilling pond and right in line with the foot valve that released water. A 20m jet of water, paired with swirling wind, makes for a tropical storm. At least, that is what it felt like at the time. One would think these conditions would be welcoming when temperatures are well into the mid to high thirties, but the sheer volume of water drenches you in seconds and the swirling wind cools you just as fast.
What we thought would be our last challenge was to get the drill rigs down into the bottom of the stilling pond. This area was however not concreted but rather a natural riverbed with boulders and mud making access extremely difficult. The only solution was to call on the excavator and a smaller 20-ton mobile crane to assist.
The same procedure was followed only this time the mobile 20-ton crane had to sling the one drill rig from the edge of the Apron down into the bottom of the stilling pond whilst the excavator created an earth access path from the top of the Apron to the bottom of the stilling pond so that the tracked drill rig could track to the borehole location. Whilst this operation was underway, the client decided they needed to investigate the area around the hydro plant; our fourth access challenge.
Space and access were restricted in this area. It required the use of the smaller drill rig which had since finished the boreholes on the elevated platforms. The MERC 4x4 crane truck returned from the laydown area with the smaller rig and its equipment. The rig had to be placed over a 1.50m high retaining wall and manually pushed into place underneath the two large water pipes feeding the hydro plant. Once all the drill rigs were in place, the excavator and 20-ton mobile crane left the Apron area so that the hydro plant could start operating again. The MERC 4x4x crane truck was left behind the wall on an elevated platform as the smaller drill rigs needed to move to a second location once the first borehole was completed.
On completion of the final boreholes, the hydro plant was shut off, the access path prepared, and the concrete beams raised for the last time. It was a mass exit of drill rigs, drilling equipment, pumps, and core trays full of rock samples destined for the core storage area. We all watched as the excavator dropped the last of the concrete beams into place and the rising flow of the turbulent water from the hydro plant as it flowed across the rocky pathway.
A project of varying challenges successfully executed due to teamwork, communication, and hard work. The Geomech Africa team living up to our name in terms of taking any sort of access challenge and overcoming this successfully.
Plot 28 Central Road
Sunrella, Lanseria
Gauteng
South Africa
Tel. +27 (0)861 436 632
Email. info@geogroup.co.za