Drilling in Tzaneen
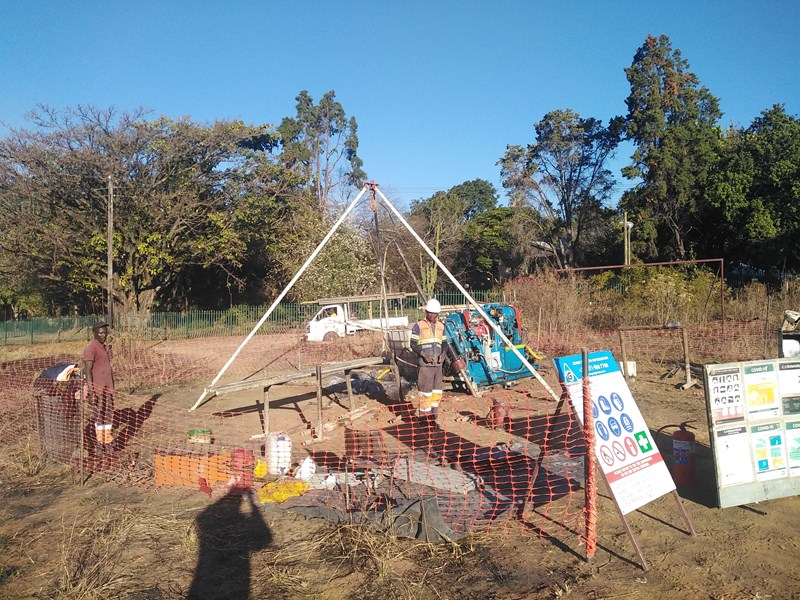
One of the greatest privileges we get to enjoy at the GeoGroup is having the opportunity to visit both local and international destinations. Although Tzaneen is only a mere 4-hour drive from our Lanseria head office, it was still a spectacular and memorable experience for Welcome Dlamini and his crew. This is the first project that Welcome had the opportunity of managing as the appointed site supervisor.
On the 14th of June, 2021, Welcome and the team commenced drilling with the mandate to conduct Geotechnical Investigations at 139 borehole locations in the area for an upcoming project using both YWE D90 & D45 drill rigs. These rigs were the design and brainchild of the late Dave Rossiter, founder and CEO of the GeoGroup.
Upon inspection of the various drill locations, the team knew that a challenge was ahead of them. On most drilling projects, access is always one of the greater challenges the team faces. To get from any main road to the area of operation, our teams must often clear the area of brush and other natural materials for the rigs, heavy vehicles, and crew to reach their destination. Specifically, on this project, the team had to clear the multiple access routes with a TLB while working next to busy roads and bridges. It goes without saying, that our teams must take every precautionary step. Not only to ensure their own safety but the safety of those around them.
As is the nature of projects in the Geotechnical Investigations field, it is often expected for our teams to run into some unforeseen challenges. Let’s have a brief look at some of these challenges the team faced on this site. One of the drill positions were located in the middle of a body of water. This proved quite difficult for the rigs and staff to reach. As a work-around, Welcome and his team had to perform some earthworks over a 2-day span by pushing soil into the water, creating a platform to act as a stability island allowing the drill to operate safely. With this game plan, the crew was able to drill this location successfully. What is important here, is that rehabilitation must take place to ensure the environment is rehabilitated back to its original form so to minimise the impact around us.
On any drilling project in the GeoGroup, we always aim to ensure top quality core is produced for our clients. As with many drill sites, ground conditions throw challenges our way, but it's important to remember our core principles in achieving our standards and quality core. At one of the drill positions located close to a main bridge in the area, some underlying boulders were encountered. The borehole kept collapsing as they were drilling, and this usually happens when the loose soil fragments fall into the hole as the drill rod is retracted. In these situations, the team would use a product called AMC CR 650™. This polymer is used to improve cuttings encapsulation and to help stabilise the formation by forming a protective polymer on the drill- bit, rods and on the walls of the borehole. It also acts as a lubricant when drilling in difficult ground conditions, thus making core extraction a lot easier. With the polymer circulating with the sump water, the team could successfully complete this drill location.
With the project running for about 3 months, our supervisor and crews were happy to return to the office without any injuries occurring on site. The project was a big success for the GeoGroup and for the site supervisor, Welcome Dlamini.
Plot 28 Central Road
Sunrella, Lanseria
Gauteng
South Africa
Tel. +27 (0)861 436 632
Email. info@geogroup.co.za