Side-By-Side in Mpumalanga
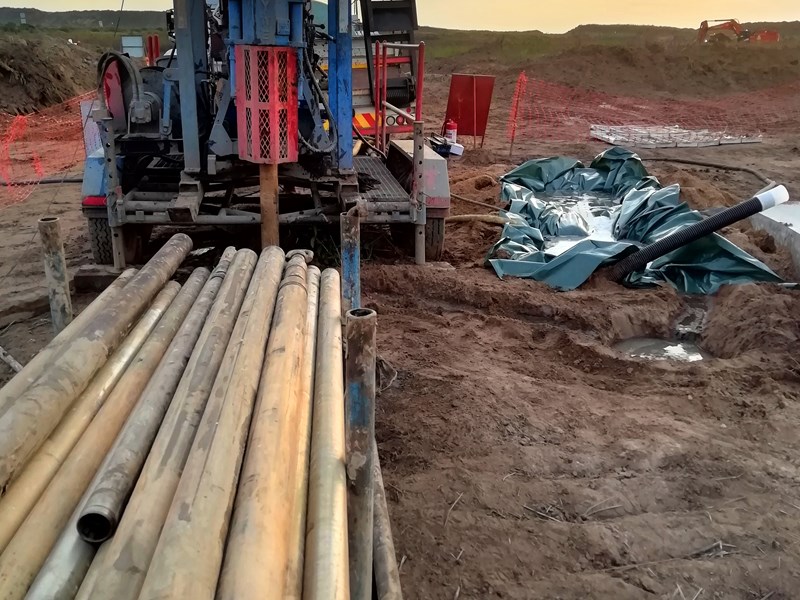
On the 27th of February 2021, the Geomech Africa and Terra Monitoring teams commenced work together for a 5-week project where they needed to conduct rotary core drilling (using a YWE-D90) at 6 locations for the installation of Piezometers at discard facilities in Mpumalanga, South Africa.
It was the mandate of the project that the Geomech Africa team were to drill the holes while the Terra Monitoring team had to install Geosense Vibrating Wire Piezometers to monitor pore pressures in zones where the softs are thicker than 20m. The client specifically requested that the data be available remotely with trigger levels for the vibrating pore pressure and low battery alarms.
To achieve this, Terra Monitoring installed ten Geosense 350kPA Piezometers at the various drill sites which connected to a 3G Campbell Scientific Data Logger that sends the data remotely to the client. The Campbell LoggerNet software, with a custom programmed RTMC graphics dashboard, was then installed on the client’s computer in the mine’s control room for real-time data logging. From this point on, the operator can then customise the reading and trigger levels from the control room. Innovatively, the system can also send alerts to 4 different phone numbers alerting them to any triggers in the readings.
For the most part, the teams were able to avoid any major delays with this project. Elijah Mahlangu, the Geomech Africa supervisor on this project, did however anticipate that the clay in the soil could possibly hinder the drilling process. “Drilling in clay-like soil can be quite difficult. That’s why one must go to site prepared. While we were drilling at one of the locations, we noticed that the water was not clearing the clay out of the barrel. We immediately knew that the clay was sticking to the inside of the barrel which meant that should we want to remove the core barrel, we were going to have a hard time pulling out the Inner tube using wireline as the clay would make it too heavy to extract. This usually happens when the sumps used to filter the water are too saturated for the water rotation. The more you drill, the more sludge mixes with your water rotations causing the same clay to block the barrel again. The solution we used was to create a third sump which allowed the first and the second sump to catch all the solid clay materials and then using the clean water in the third sump to circulate back into the hole to free the barrel from any clay sticking to it, allowing the drill bit to advance.”
Operators must also remain mindful of their environment when they are navigating sites. The last thing a crew would want is to get stuck in the mud moving from one location to the next. Most of us would think it is an easy solution to simply call for assistance. However, this is never the case on some of these sites. In the event of an incident like this, the site staff would need to be informed. Then you will always risk having to wait up to a day for a team to be dispatched to help free vehicles and rigs with a string of paperwork that would need to be completed before work can resume. A delay that can easily be prevented by following the advice of supervisor Elijah. He is a firm believer that prevention is always better than cure. He says: “When you approach a project with a proactive attitude, you will save yourself a lot of time. Because you will see most things coming before they even happen.”
In conclusion, the team was able to drill a total of 80 meters and install all the required equipment without any major delays, incidents, or accidents. Another successful project completed by the Geomech Africa and Terra Monitoring Teams.
Elijah Mahlangu has been with the GeoGroup family since 2007 where he worked as a driver and crane operator for 4 years after which he grew into the role of a site supervisor. He is highly regarded with 11-years of experience in the geotechnical drilling field.
Plot 28 Central Road
Sunrella, Lanseria
Gauteng
South Africa
Tel. +27 (0)861 436 632
Email. info@geogroup.co.za