Geo 601 dual-head drill rig improves assessment of ground conditions at tailings dams facilities
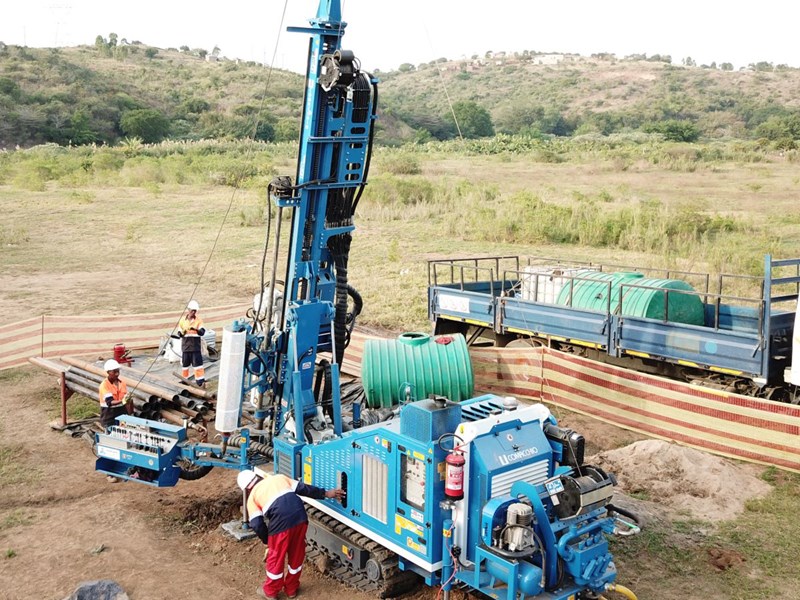
Increasing pressure on mining companies to publicly disclose information on their tailings dams highlights the need for improved technology to more accurately test dam stability and more reliably predict potential failures.
South African geotechnical services provider GeoGroup founder Dave Rossiter believes that the Geo 601 dual-head drill rig – custom-made for Geomechanics by Italian drill rig manufacturer Comacchio – is well suited to assessing ground conditions at tailings dams facilities more accurately. The sonic drilling method requires the hole to be cased in its entirety, thus providing a fully cased hole on completion which facilitates the installation of tailing dam safety monitoring instruments into the drilled hole.
Geotechnical investigations company Geomechanics – a subsidiary of GeoGroup – imported such a rig – the only one of its kind in South Africa, according to Rossiter – in 2019 at a cost of R6-million.
The Geo 601 dual-head drill rig comprises a rotary core drill head for standard core drilling applications in hard ground and a sonic drill head for softer ground conditions.
“If one wants good-quality samples for testing to better understand the potential for a tailings dam failure, then one needs to consider using sonic and rotary core drilling techniques in conjunction with each another,” Rossiter tells Mining Weekly.
The sonic head can be used to acquire good-quality samples from the soft tailings deposits in the dam, while the rotary core head can be used to drill into the hard rock beneath the dam, enabling geo-technicians to accurately record data on the interface between the two different ground conditions.
The dual-head capability negates the need for two separate rigs on site, which helps lower costs while accelerating the process.
“There is a global increase in demand for technology and instrumentation that can help avert potential tailings dam collapses,” Rossiter notes, adding that tailings policies are being scrutinised worldwide.
Conventional rotary core drilling does not automatically yield good core samples in all ground conditions, despite the use of split double- and triple-tube core barrels, as well as expensive drill muds to enhance core recoveries.
“When drilling in soft or weathered materials, it is often difficult to produce a good-quality core using conventional rotary core technology,” Rossiter explains. “This can be a source of frustration and, ironically, lost information when working in softer ground formations.”
Such information could be pertinent to the accurate assessment of tailings dam stability, he adds.
The sonic drill head allows for the soil sample to enter the single-tube core barrel by liquefying the ground on the sidewall of the sample that enters the core barrel without disturbing the sample, thereby providing good core recoveries in softer, more friable ground.
The sonic vibration is created by the resonance in the sonic drill head, which then transfers down into the drill rod and core barrel. This sonic resonance is prevented from going into the drill head and causing damage to the machine by an air spring, which isolates the vibration.
“Sample recoveries in soft-ground conditions using sonic technology are usually more than 95%,” Rossiter points out. “However, it cannot be used in hard ground formations. This is where the dual-head capability comes in handy.”
The Geo 601 drill rig can drill up to a depth of 60 m using the sonic head and a depth of 200 m using the rotary core head.
Plot 28 Central Road
Sunrella, Lanseria
Gauteng
South Africa
Tel. +27 (0)861 436 632
Email. info@geogroup.co.za